Exploring the Role of Vacuum Forming in Prototyping

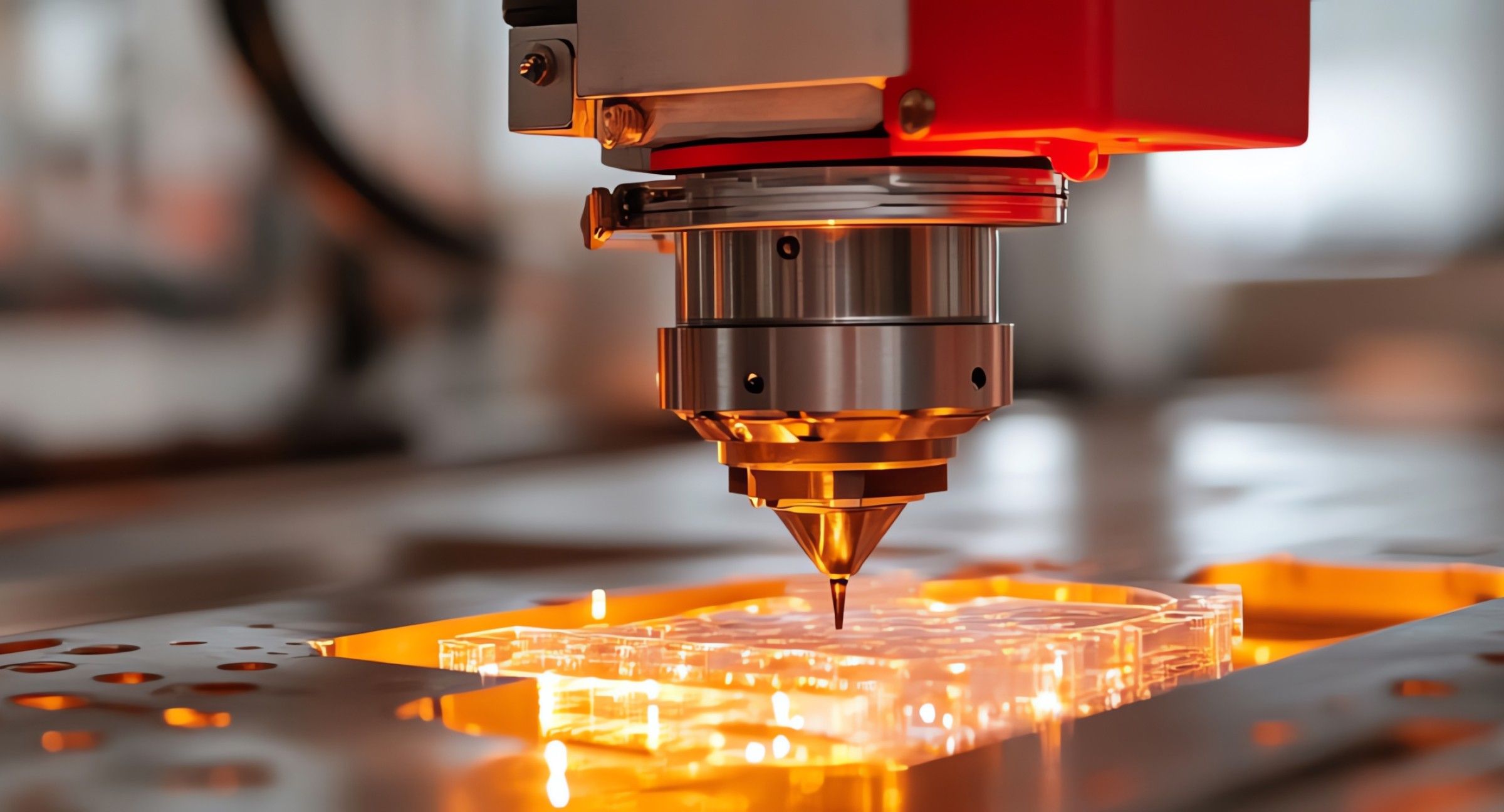
While 2D images prototyped on a computer can give you a general sense of a design, they are rarely enough to truly understand how a product will look and feel in the real world. But how do you bring your vision to life without breaking the bank? Enter vacuum plastic forming—a versatile prototyping technique we use to quickly transform your vision into a living three-dimensional form.
But how does vacuum plastic forming work? More specifically, why is this manufacturing process ideal for prototyping? We’ll explain everything here.
What Is Vacuum Plastic Forming?
Vacuum-formed products are made by heating a plastic sheet until it is pliable. After stretching it over a mold, we use vacuum pressure, pulling the plastic tight against the mold to capture fine details and maintain uniform thickness.
The Benefits of Vacuum Plastic Forming
The process of vacuum forming is ideal for prototyping for several reasons:
- Cost-efficiency: Vacuum plastic forming requires minimal tooling. Plus, molds can be made from affordable (yet effective) materials like wood, MDF, or 3D-printed plastic.
- Speed: Once the mold is made, prototypes can be manufactured in minutes.
- Detail: You deserve more than a vague rendering of your original idea. The vacuum-forming process captures fine details and quality prototypes that accurately represent the final product.
- Versatility: The vacuum plastic forming process works with a variety of materials and applications. We use this process to create prototypes using everything from food-safe PETG to tough, impact-resistant ABS.
What Makes the Vacuum Forming Process Superior?
Scale With Need
Traditional prototyping methods can be costly and time-consuming. With vacuum forming, production takes minutes, and once you have the mold, you only need inexpensive plastic sheets. This combination of speed and low material costs makes it ideal for prototyping vacuum-formed products.
Production-Ready Testing
Many prototyping methods only approximate the finished product. Sometimes, they are not even made from the same materials as the final product. In contrast, the vacuum forming process gives you a production-ready product made from the right materials.
Flexibility
Modifying your original design can be costly with traditional manufacturing methods. In some cases, it may require creating a completely new mold. Conversely, vacuum forming molds are cheaper to produce and easier to modify.
Detail & Consistency
When projects require razor-sharp detail and complex undercutting at reverse angles, traditional manufacturing methods don’t cut it. Vacuum plastic forming allows us to control material thickness, capture fine details, work with complex shapes, and ensure quality outcomes.
Our Prototyping Process
Sometimes, our team is provided with a design. Other times, we help bring a vision to life. Every project is unique. That said, here’s a general overview of how we typically prototype vacuum-formed products:
- Concept design: Have a design idea but need our team to refine it? We can help. Already have the design specs? Let’s talk about your timeline, needs, and budget to develop a prototyping plan.
- Material selection: Next, we’ll help you select the right plastic type to ensure optimal performance. We’ll use the same material in prototyping as in full-scale production.
- Mold selection: We'll help select the right mold for your project, whether it's wood, aluminum, or 3D printed. Each has its advantages depending on your specific needs.
- Production: Want refinements? No problem. Need to move to production? We've got you covered. Our quick turnaround means you can adjust your design without long delays.
From Concept to Creation: Meet the Vacuum Forming Experts
Ready to transform your vision into a prototype? We’ve got you. With nearly 30 years of experience and specialization in composite materials, fiberglass, FRP, rotocasting, tooling, mold making, and more, we have the skills and expertise to bring your project to life. Contact us today!