Five Reasons Why Fiberglass Is Best for Medical Devices

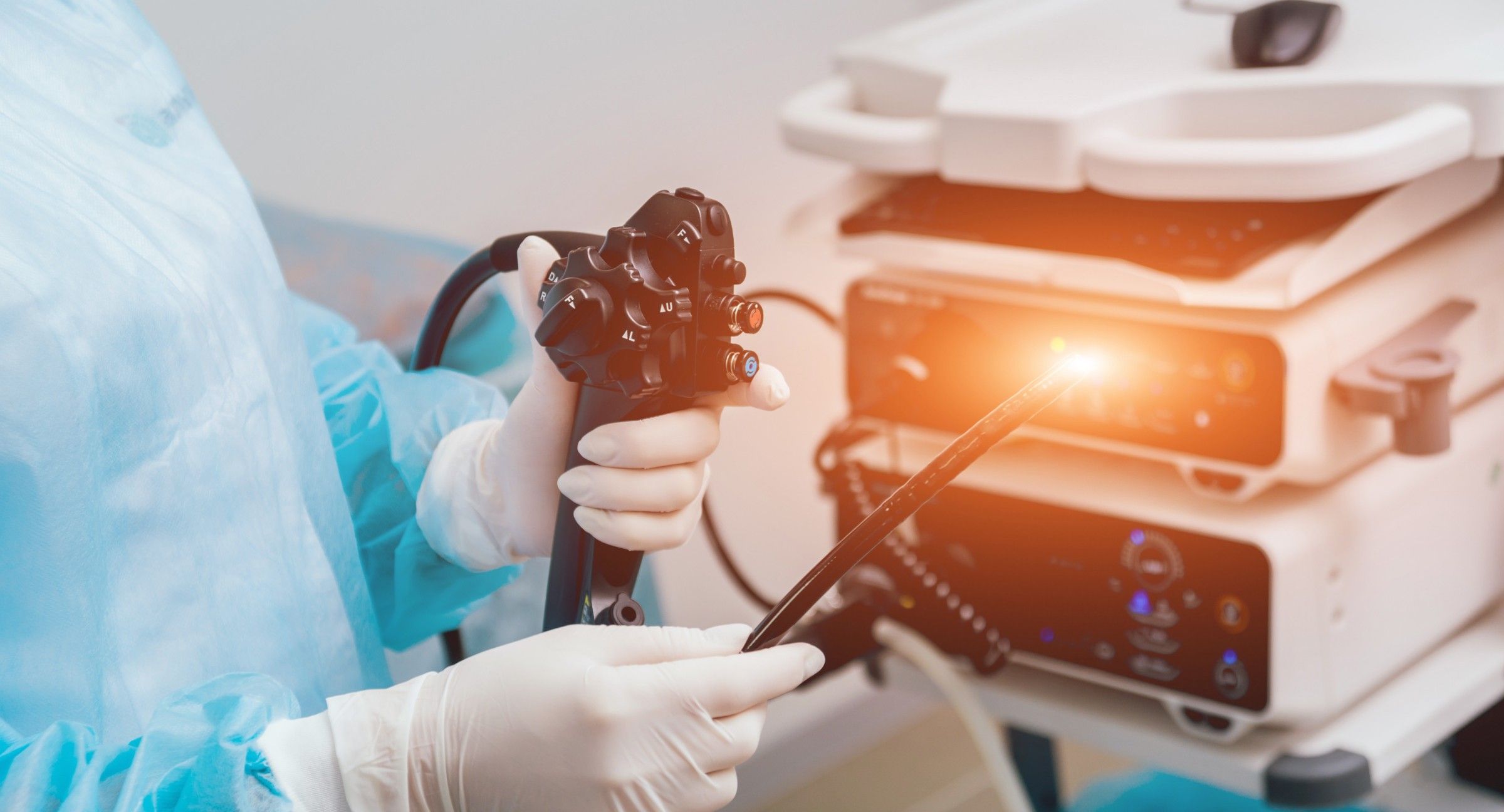
Medical device manufacturing requires precision and dependability, and fiberglass is the ideal material to meet these requirements. Its lightweight, durable and non-corrosive qualities make it the perfect choice for medical device components.
In addition to its strength and versatility, fiberglass offers several advantages over other materials used in medical device manufacturing.
From cost savings to greater safety, here are five reasons why fiberglass is best for medical devices and their manufacturing.
1. Superior Light Performance
Fiberglass is transparent, which is important when you need to see through a part. This quality is helpful in medical equipment, such as endoscopes, where you need to see inside a patient’s body.
Fiberglass is also non-scattering, so it minimizes light loss. Light is essential for quality imaging and diagnosis, so minimizing the loss of light is a must for the best images.
2. Stable at High Temperatures
Most medical device components are exposed to extreme temperatures, but this is not the case with all materials. For example, fiberglass is non-corrosive, so it’s perfect for components that must be sterile and withstand high temperatures, such as incubators and autoclaves. This material can withstand temperatures up to 1,000°F.
3. High Chemical Resistance
Fiberglass is resistant to most chemicals, which makes it ideal for medical device manufacturing. In addition, this material provides several advantages over other materials, such as increased chemical resistance.
It can withstand acids, alkalines, and more. Additionally, it is non-reactive and non-oxidizing, making it ideal for sterilization. You can also coat fiberglass with various substances, such as epoxy, to provide increased protection against chemicals.
4. Durable Yet Flexible
Fiberglass is flexible and durable, ensuring its use in many medical device components. It is lightweight yet strong, which is important for larger items like incubators and autoclaves. This material also withstands flexing and stretching, so it’s an excellent fit for load-bearing components.
5. Lots of Design Choices
Fiberglass is available in many colors, and you can customize the color by adding pigments. This feature makes fiberglass an excellent choice for aesthetic components.
In addition, fiberglass comes in various thicknesses, from less than 1/2 inch to more than 2 inches. As such, you can find fiberglass in various shapes and sizes, making it an ideal choice for most medical device applications.
Conclusion
Fiberglass is the go-to material for medical device manufacturing due to its lightweight, durable and non-corrosive properties. In addition, its superior light performance, high chemical resistance, flexibility, and wide range of design options make it the preferred choice for medical device components.
From cost savings to greater safety, fiberglass offers several advantages over other materials used in medical device manufacturing. These reasons make it easy to see why fiberglass is best for medical devices.
Contact Painted Rhino for Superior Fiberglass
At Painted Rhino, we specialize in manufacturing superior fiberglass parts and components for the medical device industry. We are committed to providing quality products with a quick turnaround time. We invite you to contact us today to learn more about how our custom fiberglass solutions can help your medical device manufacturing process.